Writer: Medha Banerjee
Table of Contents
Introduction to Manufacturing Success
In the fast-paced landscape of manufacturing, where every second counts and every inefficiency can have a significant impact on operations, the integration of real-time intelligence (RTI) has emerged as a game-changer. This paradigm shift is not merely about gathering data but about harnessing live insights to drive immediate actions and optimizations. In this blog, we delve into the pivotal role of analytics services in facilitating this transformation and explore why they are indispensable in today’s manufacturing environment.
Importance of Real-Time Manufacturing Intelligence
Real-time intelligence in manufacturing transcends traditional data analysis methodologies by providing an instantaneous and dynamic view of operations directly from the factory floor. Unlike retrospective approaches that analyze historical data post-production, RTI empowers manufacturers with actionable insights in the moment, enabling faster response to critical issues and proactive decision-making.
Addressing Challenges with Analytics Services
While you are looking out for solutions using real-time intelligence, it is imperative that you also look into the challenges that they bring to the table. Some of them are as described below;
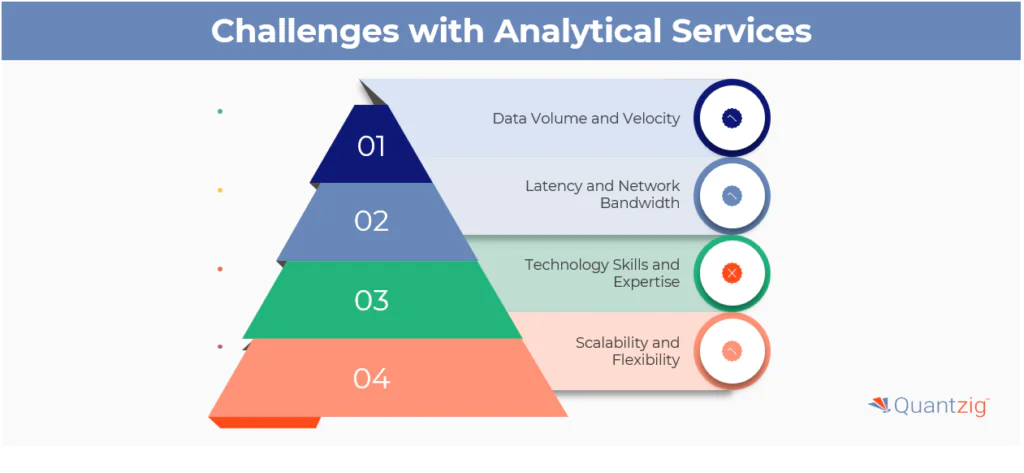
- Data Volume and Velocity
Continuous data streams from sensors and various sources pose a challenge in terms of efficient management and analysis. Analytics services offer robust infrastructure and advanced processing tools to handle the overwhelming volume and velocity of data effectively.
- Latency and Network Bandwidth
High-frequency data transmission necessitates reliable and high-bandwidth network infrastructure to ensure real-time responsiveness. Analytics services optimize network resources and minimize latency, enabling seamless data transmission and analysis.
- Technology Skills and Expertise
Implementing and maintaining RTI systems requires personnel with specialized skills in data analytics, AI, and related technologies. Analytics services provide the necessary expertise and support to navigate the complexities of RTI implementation, ensuring optimal performance and functionality.
- Scalability and Flexibility
RTI systems must be scalable to accommodate future growth and adaptable to changing production processes. Analytics services offer scalable solutions that evolve alongside manufacturing operations, providing flexibility and agility to meet evolving demands.
Also read: Tech Innovation: A Preview of Our Next Product Analytics Feature
Book a demo to experience the meaningful insights we derive from data through our analytical tools and platform capabilities. Schedule a demo today!
Request a Free DemoUnlocking Intelligent Manufacturing Solutions and Value with Quantzig Services
Quantzig’s Manufacturing Analytics suite, coupled with innovative Digital Twinning & Manufacturing AI solutions, offers a multitude of benefits for manufacturers:
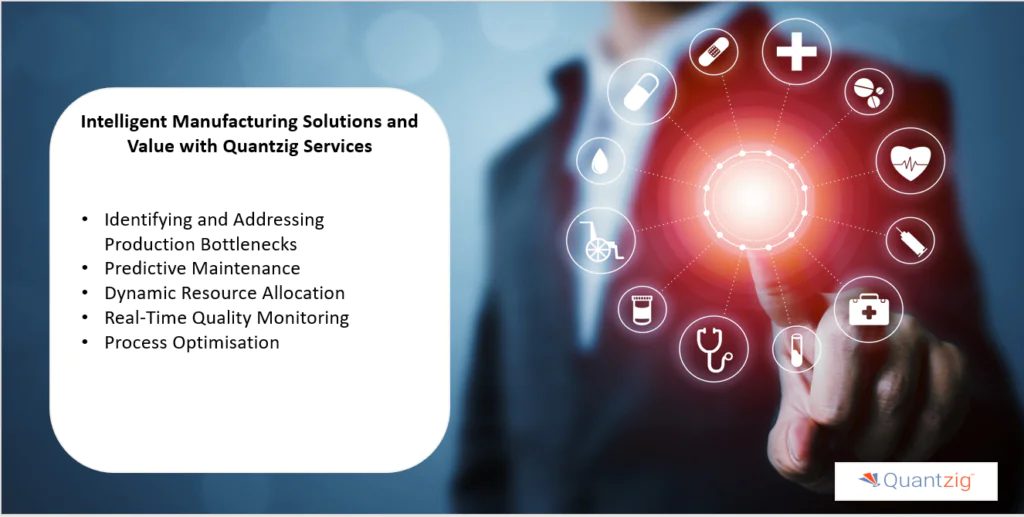
- Identifying and Addressing Production Bottlenecks: Pinpointing machines with reduced output or quality issues enables immediate corrective action, minimizing downtime and optimizing production flow based on the metrics.
- Predictive Maintenance: By analyzing sensor data, RTI anticipates potential equipment failures and schedules preventative maintenance, minimizing disruptions and saving costs.
- Dynamic Resource Allocation: Real-time adjustment of material flow, staffing levels, visualisation, and machine scheduling maximizes resource utilization and efficiency.
- Real-Time Quality Monitoring: Immediate detection of product defects allows for corrective actions, reducing waste and rework costs.
- Process Optimisation: Continuous monitoring of metrics and adjustment of production parameters based on real-time feedback ensure consistent product quality, visualisation and adherence to specifications.
Read More: Enhancing cash distribution with forecasts and levels for a retail bank
Experience the advantages firsthand by testing a customized complimentary pilot designed to address your specific requirements. Pilot studies are non-committal in nature.
Request a free PilotHow you can maximize Manufacturing Efficiency with Real-Time Analytics Solutions
By leveraging cutting-edge real-time manufacturing analytics solutions and automation, companies are now able to streamline operations, enhance productivity, and drive informed decision-making across all levels of the organization. Let’s delve into the manifold benefits of adopting these innovative solutions and how they address the pressing needs of modern manufacturing businesses.
Unifying Operations in Manufacturing Intelligence with Real-time Manufacturing Analytics
- Single Source of Information
In traditional manufacturing setups, siloed departments and disparate systems hinder seamless communication and decision-making. Real-time manufacturing analytics systems serve as a cohesive platform with automation, connecting all departments and stakeholders involved in production processes. By standardizing methodologies and reporting procedures, these systems provide a unified view of operations across multiple factory sites, fostering trends and a data-driven decision-making culture.
- Reports and Dashboards
To facilitate instant inventory decision-making, real-time production efficiency software offers customizable reports and dashboards tailored to individual user needs. These comprehensive performance updates and comparative analysis charts empower managers to identify and address issues proactively, mitigating potential inventory disruptions before they escalate.
- Real-Time Smart Alerts
With real-time smart alerts, deviations from pre-set Key Performance Indicators (KPIs) are detected instantaneously, enabling swift corrective action. Operators and managers receive automated notifications, allowing them to maintain process stability and prevent costly downtime or quality issues.
- Improved Transparency
Transparent information flow enhances visibility across all manufacturing operations, simplifying task management and facilitating smooth transitions during personnel shifts. Real-time shop floor analytics ensure that incoming personnel are quickly briefed on production status and any special concerns, strengthening operational transparency both internally and externally with customers.
Enhancing Efficiency and Minimizing Waste with Data Analytics in Manufacturing Industry
- Higher Production Efficiency, Less Waste
Real-time production efficiency software plays a pivotal role in optimizing floor operations and maximizing Overall Equipment Efficiency (OEE). By identifying and eliminating slowdowns, scheduling predictive maintenance, and monitoring energy consumption, manufacturers can enhance productivity while minimizing waste and energy costs.
- Root Cause Analysis
In the event of OEE losses, real-time manufacturing analytics solutions enable rapid root cause analysis by analyzing production data in real time. By tracking KPIs and related actions, manufacturers can pinpoint the source of issues such as equipment failures or delays, facilitating timely interventions to mitigate losses.
- Secure Data Transfer
As manufacturing processes embraces cloud-based analytics solutions, ensuring data security and transfer speed becomes paramount. Cloud-based platforms offer secure, independent networks that encrypt manufacturing data, safeguarding sensitive information while facilitating seamless data exchange between the shop floor and the cloud.
Empowering Decision-Making and Driving Business Success for manufacturing analytics
Real-time manufacturing processes analytics solutions not only optimize production cycles but also empower informed decision-making at every level of the organization. By providing up-to-the-minute insights and actionable intelligence, these solutions enable manufacturers to make strategic adjustments in real time, enhancing operational efficiency and strengthening customer relationships.
To put it simply, real-time manufacturing analytics solutions are revolutionizing the manufacturing industry, offering unparalleled capabilities to drive productivity, minimize waste, and optimize performance. By embracing these innovative technologies, manufacturers can navigate the complexities of modern production environments with confidence, achieving new heights of efficiency and competitiveness in today’s fast-paced market landscape.
Explore our wide range of customized, consumption-driven analytical solutions services built across the analytical maturity levels.
Start Your free TrialKey Metrics Tracked in Real-time for Manufacturing Analytics
Real-time analytics has placed itself as a game-changer. By tracking key metrics in real-time, manufacturers can ensure efficient operations, higher quality products, and better customer satisfaction. Here’s how the various aspects of real-time manufacturing analytics play a crucial role:
Data Collection and Integration
The foundation of real-time manufacturing analytics lies in data collection and integration. Advanced sensors and IoT devices gather data from machines, processes, and systems throughout the manufacturing plant. This data is then integrated into a central platform, often using data lakes or other storage solutions. With this integrated data, manufacturers can gain a holistic view of their operations, including equipment performance, production rates, and quality metrics.
Analyzing Production Performance
Real-time analytics allows manufacturers to monitor production performance at all times. Metrics such as cycle time, throughput, and yield provide insights into the efficiency and effectiveness of production lines. By tracking these metrics, manufacturers can quickly identify bottlenecks, inefficiencies, or deviations from expected performance. This empowers them to make data-driven decisions for process improvements, leading to higher productivity and reduced costs.
Predictive Analytics for Maintenance and Quality Control
Predictive analytics plays a vital role in maintenance and quality control. By analyzing historical and real-time data, manufacturers can predict when equipment might fail or require maintenance. This helps prevent unexpected downtime and reduces maintenance costs. Additionally, predictive analytics can identify trends that could impact product quality, allowing manufacturers to adjust processes proactively to maintain high standards and minimize defects.
Optimizing Inventory Management
Real-time analytics helps optimize inventory management by providing up-to-date information on raw materials, work-in-progress, and finished goods. Manufacturers can track inventory levels and movement in real-time, allowing them to balance supply and demand effectively. This prevents overstocking and understocking issues, reduces carrying costs, and ensures that production runs smoothly without interruption.
Real-time Reporting and Dashboards
Real-time reporting and dashboards present the data collected in an easily digestible format, making it accessible to key stakeholders across the organization. Customizable dashboards allow users to monitor the metrics that matter most to them, from overall production performance to specific equipment status. This level of visibility supports better decision-making, swift action on emerging issues, and continuous improvement in manufacturing operations.
In summary, real-time manufacturing analytics provides manufacturers with the data and insights needed to operate efficiently, maintain high-quality standards, and respond quickly to changes in demand or production conditions. By leveraging key metrics across data collection and integration, production performance, predictive analytics, inventory management, and real-time reporting, manufacturers can drive their operations to new levels of success.
Conclusion
In conclusion, real-time intelligence is revolutionizing the manufacturing industry, offering unprecedented insights and opportunities for optimization. Analytics services play a pivotal role in harnessing the full potential of RTI, addressing challenges, and unlocking value for manufacturers. By leveraging Quantzig’s advanced solutions, manufacturers can stay ahead in the competitive landscape, driving efficiency, innovation, and profitability in their operations.