Written By: Sudeshna Ghosh
In the dynamic landscape of modern manufacturing, achieving optimal efficiency is paramount for sustaining competitiveness. This article delves into the intricacies of enhancing operational performance through the strategic utilization of Capacity Planning within ERP systems. As businesses strive to meet the demands of a rapidly evolving market, understanding the transformative potential of Capacity Planning becomes imperative. This comprehensive article navigates through the nuances of this powerful tool, shedding light on its role in streamlining production processes, mitigating bottlenecks, and ultimately bolstering overall manufacturing efficiency. In a world where precision and agility are prerequisites for success, this article serves as an indispensable guide for industry professionals seeking to harness the full potential of Capacity Planning within their ERP frameworks.
So, don’t miss out on the opportunity to revolutionize your approach to efficiency – read on and empower your manufacturing endeavors today!
Book a demo to experience the meaningful insights we derive from data through our analytical tools and platform capabilities. Schedule a demo today!
Request a Free DemoTable of Contents
What is Capacity Planning in Manufacturing?
Manufacturing capacity planning, a crucial aspect of business operations in the manufacturing industry, involves forecasting demand, analyzing production lines, and optimizing production processes to maximize efficiency. Through methods such as rough cut capacity planning and resource planning, manufacturers strategically allocate resources, considering workforce capacity and equipment capacity. This ensures that production plans adhere to the organization’s production processes while maximizing output and minimizing inefficiencies.
One of the primary objectives of manufacturing capacity planning is to ensure that production plans align with available capacity, avoiding issues like overcapacity, excess inventory, and missed delivery dates. By integrating advanced planning and scheduling (APS) systems, manufacturers can dynamically adjust production plans in response to changing variables, optimizing supply chain capacity and production efficiencies.
Manufacturing capacity planning relies on comprehensive data from various sources, including supply chain capacity, inventory management, and production rates. Modern manufacturing ERP systems facilitate this complex process by providing real-time insights and enabling proactive decision-making. Overall, effective capacity planning is essential for maintaining competitiveness in the manufacturing landscape and meeting customer demands efficiently.
The 3 Types of Manufacturing Capacity Planning
Before proceeding, it’s essential to understand the three primary types of capacity planning in manufacturing. Establishing a plan is crucial to ensuring optimal current resource use and preparing for changes in demand.
Workforce capacity planning
It ensures adequate team members are available to meet production demands, optimizing current resource use. It involves aligning people with customer needs while considering market conditions to maintain customer satisfaction. Utilizing platforms for shop floor operations enhances workforce planning effectiveness. Additionally, prioritizing a healthy workplace environment prevents exhaustion and burnout, sustaining worker morale and quality of work. Efficient workforce capacity planning is crucial for meeting customer orders promptly and fostering long-term success.
Equipment capacity planning
It focuses on managing drilling machinery and other assembly line components to optimize capacity utilization. It ensures the availability and efficient use of equipment to meet production demands and complete customer orders promptly. Proper equipment capacity planning minimizes manufacturing costs and maximizes overall operational efficiency. Investing in suitable systems and technology facilitates effective monitoring and maintenance of equipment, ensuring smooth production processes and customer satisfaction.
Product capacity planning
It involves managing customer orders and raw materials to meet customer satisfaction and maintain quality of work. It ensures that adequate raw materials are available to complete orders efficiently while minimizing manufacturing costs. Implementing effective product capacity planning strategies requires robust systems for tracking and monitoring inventory and production processes. By aligning product capacity with customer demands, businesses can optimize resource utilization and enhance overall operational performance.
Importance of Capacity planning in the manufacturing industry landscape
In the dynamic manufacturing landscape, success hinges on a transparent grasp of production capacity. This understanding facilitates efficiency maximization via enhanced scheduling, balanced workloads, and resource optimization, culminating in improved profitability. The positive ripple effect extends to increased resilience, agility to adapt to demand shifts, heightened customer satisfaction rates (CSAT), and informed investment decisions in the medium term. In the ever-changing manufacturing realm, comprehending these facets proves vital, empowering businesses to not just fulfill but exceed industry norms. Prioritizing a clear overview of production capacity is more than a strategic choice; it becomes the cornerstone for sustained success, ensuring enterprises are poised for excellence and adaptability in an ever-evolving market.
Capacity planning holds immense significance within the manufacturing industry landscape as it facilitates efficient utilization of resources, enhances production processes, and ensures optimal production efficiencies. By integrating demand forecasts and analyzing production lines and processes, businesses can strategically allocate resources through resource planning and various types of capacity planning such as workforce and equipment capacity planning. This not only streamlines inventory management but also enables effective production management and achievement of desired production rates. Moreover, capacity planning plays a vital role in mitigating risks associated with over or underutilization of resources, thus contributing to improved production efficiencies and overall supply chain capacity. Leveraging advanced tools like manufacturing ERP and Advanced Planning and Scheduling (APS) systems further enhances the effectiveness of capacity planning, allowing organizations to optimize their production plans and maintain a competitive edge in the market.
Key Capabilities of Capacity Planning in Manufacturing
Manufacturing capacity planning encompasses essential functions within business operations, particularly in the context of demand forecast and optimizing production lines and processes. Through tools like rough cut capacity planning and resource planning, manufacturers strategically allocate resources, including workforce capacity and equipment capacity, to maximize efficiency. Effective inventory management is crucial for ensuring smooth production management and achieving desired production rates.
One of the key capabilities of manufacturing capacity planning is its analytical modeling feature, which utilizes advanced algorithms to track production efficiencies and adjust production plans accordingly. Simulation modeling allows for the exploration of various scenarios, helping planners identify potential bottlenecks and optimize supply chain capacity. Incorporating actual capacity data ensures accuracy in production capacity planning and enables the identification of systemic issues and assembly line components.
Moreover, advanced planning and scheduling (APS) systems play a pivotal role in manufacturing ERP, facilitating dynamic adjustments in response to changes in organization’s production processes and product capacity planning. By continually revising production plans based on actual values, APS-based capacity planning ensures efficient resource utilization and minimizes wait times between production processes. Overall, the integration of comprehensive data and advanced algorithms in manufacturing capacity planning is crucial for enhancing productivity and maintaining competitiveness in the manufacturing landscape.
What are the challenges while implementing capacity planning in manufacturing?
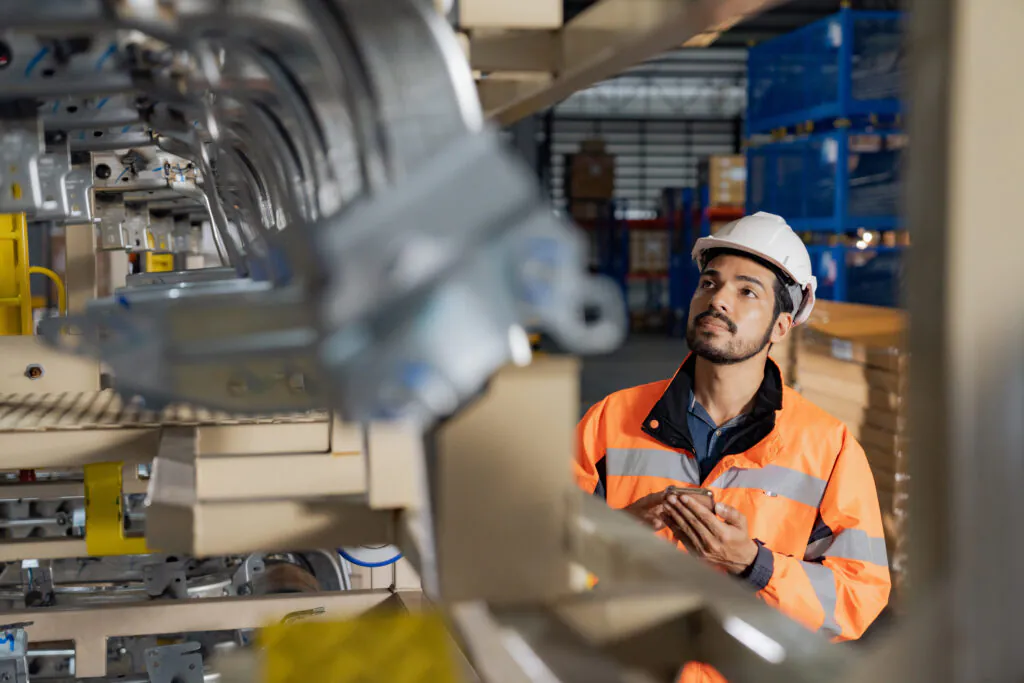
Capacity planning in manufacturing, while pivotal, presents its own set of challenges. Firstly, grappling with demand uncertainty poses a significant hurdle, given the complexities of accurately predicting future demand. Factors such as economic trends, seasonality, and competitor activity introduce instability to forecasts, resulting in challenges like underproduction or excess production.
Secondly, the necessity for comprehensive data on various aspects like labor availability, equipment performance, and material lead times is impeded by data silos and inaccuracies residing in different systems. Lastly, the implementation of effective capacity planning in manufacturing entails the adaptation of workflows, coordination of diverse teams, and integration of new technologies, which can be particularly daunting in large or intricate manufacturing operations. Addressing these challenges becomes imperative to ensure an optimized and seamless capacity planning in manufacturing process in the manufacturing sector.
Best Practices of Manufacturing Capacity Planning
Effective manufacturing capacity planning is critical for organizations to optimize resources, meet customer demand, and maintain competitiveness in today’s dynamic market. By strategically aligning production capabilities with business objectives, companies can streamline operations, enhance efficiency, and achieve sustainable growth. In this context, implementing best practices in manufacturing capacity planning becomes essential. Below, we explore five key benefits of adopting these practices to drive success in manufacturing operations.
1. Implement Leaner Operations:
Optimize resource utilization by identifying and eliminating bottlenecks in production. Utilize MES software for real-time monitoring and bottleneck management. Implement buffers for learning and development to enhance staff qualifications and overall project management maturity. Streamline administrative tasks through automation, freeing up time and level of effort for strategic planning. By focusing on lean principles, businesses can achieve on-time delivery and maximize actual output while minimizing discrepancies and delays.
2. Utilize Advanced Analytical Modeling:
Leverage analytical modeling to accurately assess anticipated demand and forecast production resources requirements. Incorporate simulation modeling to simulate various scenarios and anticipate bottlenecks in production. Implement buffers for L&D to enhance staff qualifications and improve project management maturity. By integrating these models into manufacturing lead time calculations, businesses can achieve better resource utilization and streamline production cycles for improved efficiency.
3. Invest in Integrated Software Solutions:
Implement MES software to centralize data collection and communication across the factory. Utilize integrated business tools and platforms for seamless coordination of purchase and sales orders and prioritization of priority projects. Leverage integrations to connect production orders with sales performance data for better forecasting and planning. By utilizing a central intuitive platform, teams gain full visibility into operations, enabling proactive decision-making and optimizing time tracking and task completion times.
4. Focus on Continuous Improvement:
Establish a culture of continuous improvement by prioritizing best practices and regularly assessing project management maturity. Implement leaner operations to eliminate waste and improve efficiency, supported by real-time data analysis and communication. Encourage staff qualifications enhancement through learning and development initiatives, fostering a skilled workforce capable of adapting to changing market conditions. By continually refining processes and addressing challenges proactively, businesses can achieve maximum potential output and maintain a competitive edge.
5. Ensure Data Accuracy and Granularity:
Prioritize data accuracy and granularity to enhance the effectiveness of forecasting demand and optimizing production capacity. Implement robust systems for data collection and analysis, capturing critical resources and production or workstation estimates accurately. Utilize software solutions with comprehensive reporting capabilities to identify bottlenecks in production and areas for improvement. By ensuring true availability of resources and maintaining high standards of data granularity, businesses can make informed decisions, minimize manufacturing costs, and achieve sustainable growth.
How does Quantzig’s Capacity Planning in ERP provide Benefits in the manufacturing industry?
Effective capacity planning in manufacturing involves analyzing workforce capacity and equipment capacity to ensure optimal utilization of resources. By considering assembly line components and product capacity planning, manufacturers can align production with organization’s production processes and meet demand efficiently. Utilizing finite capacity planning methodologies enables accurate assessment of production limits, minimizing bottlenecks. Through strategic production capacity planning, companies can optimize workflows and maintain competitiveness in the market. Overall, a comprehensive approach to capacity planning integrates workforce, equipment, and production considerations to drive operational excellence.
Empower your manufacturing efficiency with our dynamic planning solutions, meticulously tailored at the site, category, and line levels, facilitating time-efficient and agile planning. Our comprehensive manufacturing optimization solution is driven by four pivotal components, each engineered to elevate your operational prowess.
- Cost Determination Analysis: Uncover the true cost per unit with an exhaustive analysis, encompassing pallet holding, risk of wastage, and binding costs. Gain a competitive edge by understanding and optimizing the complete cost landscape.
- Demand Leveling Module: Revolutionize your demand management by leveling processes across products. This strategic module aims to reduce demand variation while concurrently minimizing costs and variability, ensuring a cost-effective and streamlined production pipeline.
- Automation: Embrace efficiency with our automated scheduling optimization setup. This component recommends the lowest-cost schedule to fulfill your order plans, training requirements for manufacturing schedule planning, and drastically reducing manual efforts. Stay ahead in the automation era.
- Scheduling Optimization: Fine-tune the sequencing of manufacturing and packaging across shifts with our scheduling optimization feature. Witness reduced labor costs, minimized wastages, and swifter switchover times, enhancing overall operational efficiency.
Discover how Quantzig’s capacity planning transforms the manufacturing industry, providing unparalleled customization, agility, and optimization across every facet of your production process. Elevate your manufacturing capabilities with our cutting-edge solutions.
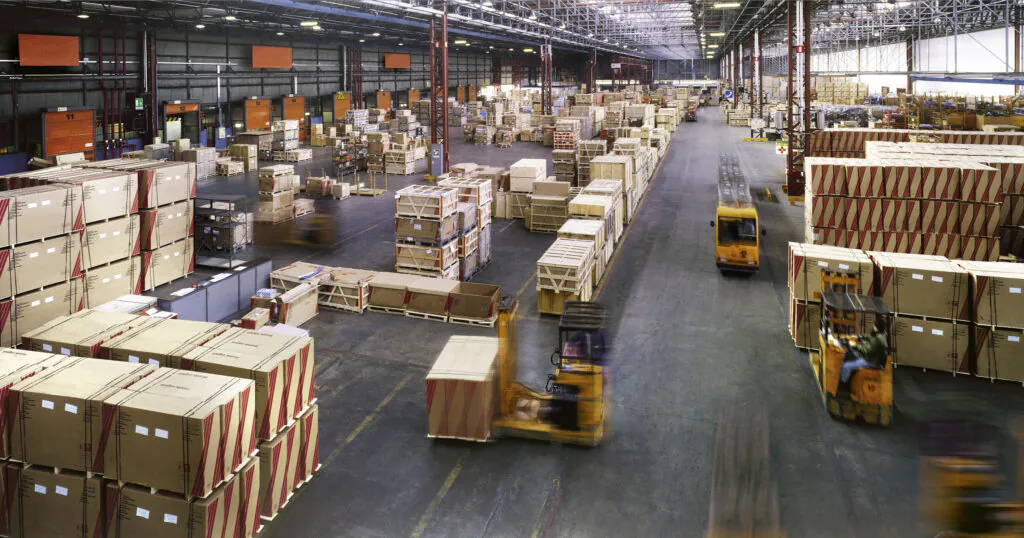
Quantzig’s Success Story:
Client location:
UK
Challenges faced by the client:
A UK-based food and beverage retailer, specializing in ready-made meals and various food products, confronted distinctive challenges in their production processes. Each product line adhered to a specific recipe, with unique nuances observed throughout the production journey, spanning from ingredient preparation to packaging. The complexity arose from the need to plan for fluctuating demand across diverse stores and sites within the manufacturing plant. The existing planning process proved to be unpredictable, resulting in challenges such as surplus production, excess inventory, and shortages occurring in various locations. The erratic nature of the incumbent process made it difficult for the client to effectively match production with demand, leading to imbalances in inventory levels and impacting overall operational efficiency.
Solutions offered by Quantzig:
Quantzig provided the client with a comprehensive planning solution that served as a centralized platform for interacting, forecasting, simulating, and updating plans seamlessly back into SAP, thereby ensuring a streamlined production process. The solution comprised modules addressing various facets, including Capacity & Production Planning, Material Planning, Resource Planning, and Scheduling.
The incorporation of a long-range planning view allowed for strategic foresight, while features such as the Raw Material Planner and Production Editing & Assembly Editing modules enhanced the efficiency of resource utilization. Moreover, the solution offered intelligence tools to stakeholders, featuring a production simulator, Bill of Materials (BOM) Calculator, and a robust reporting suite.
Quantzig’s tailored solution not only addressed the client’s complex challenges related to varied demand across different stores and sites but also facilitated a more agile and responsive production process. By seamlessly integrating with SAP, the solution ensured real-time adaptability, reducing the incidence of excess production, over-inventory, and shortages. The intelligent tools provided stakeholders with enhanced decision-making capabilities, contributing to a more optimized and efficient manufacturing operation for the client.
Experience the advantages firsthand by testing a customized complimentary pilot designed to address your specific requirements. Pilot studies are non-committal in nature.
Request a Free PilotImpact Delivered
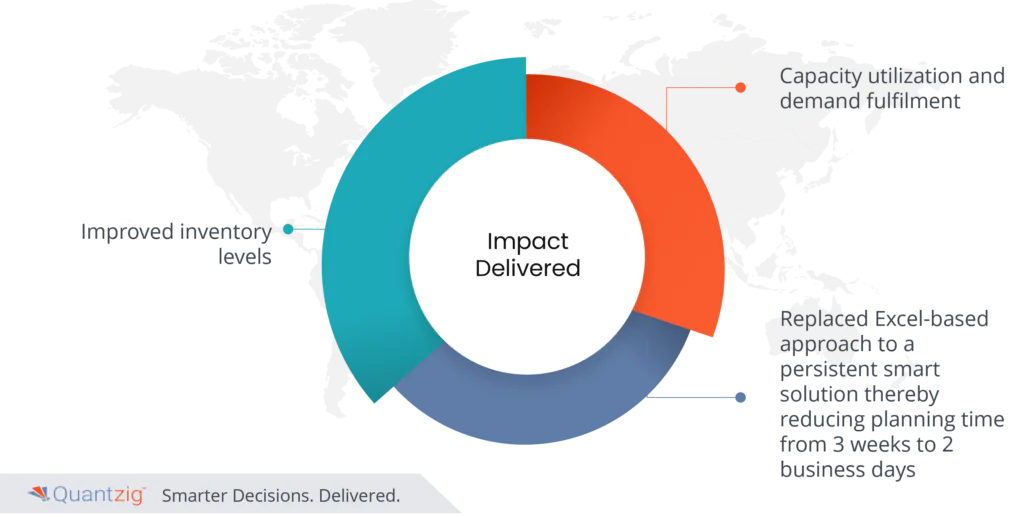
- Improved inventory levels,
- Capacity utilization and demand fulfillment.
- Replaced Excel-based approach to a persistent smart solution thereby reducing planning time from 3 weeks to 2 business days.
Technologies used:
Microsoft Azure Data Lake, Databricks, Power Apps, Power BI
Conclusion
In conclusion, the article underscores the critical role that Capacity Planning plays in the dynamic landscape of modern manufacturing. Through a meticulous examination of this strategic tool, businesses gain insights into maximizing operational efficiency, mitigating bottlenecks, and achieving agile responsiveness to demand fluctuations. The integration of Capacity Planning within Enterprise Resource Planning (ERP) systems emerges as a transformative force, empowering organizations to navigate the complexities of production with precision. As industries strive for excellence, this article serves as a beacon, illuminating the path toward enhanced resilience, cost-effectiveness, and customer satisfaction. By understanding and harnessing the power of Capacity Planning, manufacturers can not only meet but exceed industry standards, fostering a future-ready approach that propels them toward sustained success in the ever-evolving manufacturing landscape.
Get started with your complimentary trial today and delve into our platform without any obligations. Explore our wide range of customized, consumption driven analytical solutions services built across the analytical maturity levels
Start your Free Trial