Author: Associate Vice President, Analytics and Data Strategy, Quantzig.
Table of Contents
Introduction to Strategic Capacity Planning
In today’s fiercely competitive global marketplace, the key to success for manufacturers lies in their ability to not only meet but exceed customer demand while maintaining operational efficiency. The article delves into the pivotal role of capacity planning as a driving force behind sustainable growth and profitability. In an era where market dynamics are ever evolving, this article illuminates the critical strategies and innovative approaches that empower manufacturers to optimize their production capabilities, align them with customer needs, and unleash their full potential. As we navigate the complex landscape of modern manufacturing, this article serves as a beacon guiding industries toward a brighter, more prosperous future.
Request a demo to experience the meaningful insights we derive from data through our analytical tools and platform capabilities. Schedule a demo today!
Request a Free DemoWhat is Strategic Capacity Planning?
Strategic capacity planning is a critical process in manufacturing that aims to align a company’s production capabilities with anticipated demand. It involves analyzing factors like equipment, personnel, and materials to determine the optimal level of capacity needed to meet customer orders efficiently and profitably.
Importance of Strategic Capacity Planning in Manufacturing
In the landscape of manufacturing, strategic capacity planning stands as a cornerstone for operational excellence and sustainable growth. This meticulous process involves aligning resources and production capabilities with anticipated demand, ensuring efficiency, and responsiveness to market dynamics. Here’s a closer look at the paramount importance of capacity planning, weaving through the keywords relevant to the manufacturing landscape.
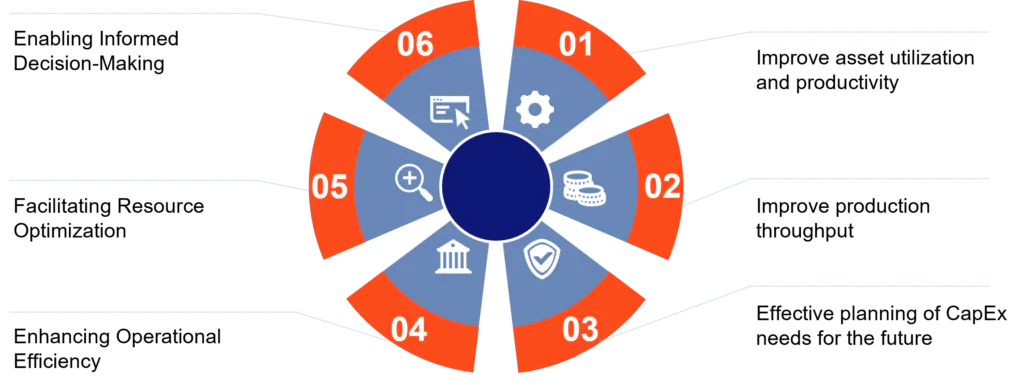

1. Improve asset utilization and productivity
- Capacity planning optimizes resource utilization by aligning production capacity with actual demand. Through meticulous demand forecast analysis, businesses can streamline operations on the shop floor, effectively managing personnel, machines, and other resources.
- This approach not only reduces lead times but also enhances efficiency and workflow, ultimately leading to reduced costs and minimized bottlenecks. By maximizing product capacity, companies can meet customer orders promptly, ensuring customer satisfaction and bolstering their competitive edge.
2. Improve production throughput
- Strategic Capacity Planning ensures timely production and delivery, thus enhancing production efficiencies and minimizing idle machinery. By accurately forecasting demand, manufacturers can maintain optimal inventories and allocate staff qualifications judiciously.
- This proactive approach mitigates production bottlenecks and optimizes resource utilization, fostering leaner operations and enabling on-time delivery. With full visibility into actual capacity and streamlined processes, businesses can respond swiftly to changes in demands, securing customer loyalty and market share.
3. Effective planning of CapEx needs for the future
- Capacity planning guides Capital Expenditure (CapEx) decisions, enabling manufacturers to allocate resources strategically. By analyzing setup time, maintenance downtime, and other production parameters, companies can prioritize investments in manufacturing machines and workstations.
- This forward-looking approach minimizes changeovers and cleaning operations, ensuring efficient use of resources and optimal production work in progress. By aligning resource capacity with long-term goals, businesses can navigate market uncertainties with confidence, driving sustainable growth and profitability.
4. Enhancing Operational Efficiency:
- Capacity planning facilitates the optimization of resources on the shop floor, ensuring streamlined workflow and reduced lead times. By leveraging data-driven demand forecasts and metrics, businesses can identify and address bottlenecks in production, minimizing product shortages and enhancing customer satisfaction.
- Moreover, efficient allocation of personnel and machines based on short-term and long-term goals fosters a culture of continuous improvement and adherence to best practices. This approach not only reduces costs but also maximizes actual output, unlocking the full potential of the factory while capitalizing on growth opportunities.
5. Facilitating Resource Optimization:
- Strategic Capacity Planning empowers businesses to optimize equipment and assembly line components, aligning product capacity with available raw materials and products. By analyzing current resource use and implementing recommendations for capacity planning, companies can enhance efficiency and mitigate production bottlenecks.
- Furthermore, proactive maintenance schedules and efficient changeovers minimize idle machinery and cleaning operations, ensuring smooth production workflows and timely work in progress. This streamlined approach not only maximizes resource utilization but also fosters leaner operations and consistent on-time delivery.
6. Enabling Informed Decision-Making:
- Capacity planning equips businesses with actionable insights, enabling informed decisions regarding forecast demand and resource allocation. By leveraging advanced software solutions such as manufacturing ERP and inventory management platforms, companies can achieve full visibility into production management and purchase orders.
- This integrated approach allows for seamless integrations with various business tools and platforms, including QuickBooks Online, Shopify, and Xero, creating a central intuitive platform for efficient manufacturing operations. Moreover, by prioritizing projects based on project management maturity and data granularity, businesses can proactively address critical resources and optimize project estimates, driving sustainable growth and long-term success.
Strategic capacity planning is indispensable for manufacturers, offering a roadmap to cost efficiency, customer satisfaction, and long-term viability. By leveraging data-driven insights and adopting best practices, businesses can navigate challenges, seize opportunities, and thrive in the ever-evolving landscape of manufacturing.
The Significance of Workforce Capacity Planning in Manufacturing
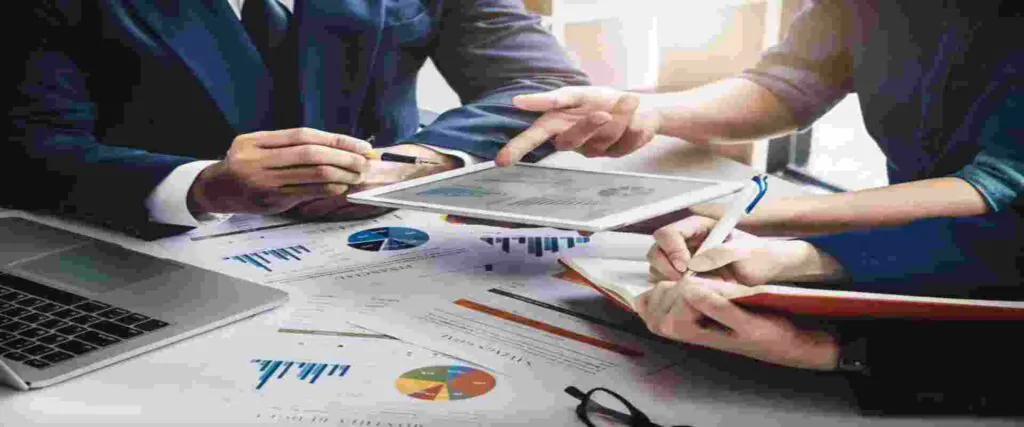
As businesses strive to meet fluctuating demands and navigate evolving market dynamics, the role of capacity planning in optimizing personnel and machines cannot be overstated.
1. Comprehensive Assessment of Projects, Lead Times, and Resource Use
- Businesses must analyze data granularity and make recommendations for capacity planning
- This allows for judicious allocation of resources to maximize efficiency and minimize bottlenecks
2. Strategic Workforce Rough Cut Capacity Planning
- Aligns short-term goals and long-term objectives
- Fosters a culture of continuous improvement and operational excellence
3. Leveraging MES Software and Communication Platforms
- Facilitates real-time collaboration among team members
- Enables swift decision-making and proactive resource allocation
4. Prioritizing Projects and Optimizing Hours/Equipment Capacity
- Enhances workflow and mitigates production bottlenecks
- Bolsters customer satisfaction and on-time delivery
5. Transcends Resource Allocation, Embodies Strategic Mindset
- Optimizes resource utilization and enhances productivity
- Provides full visibility into production processes
- Drives sustainable growth and competitiveness
In summary, effective workforce capacity planning is a strategic imperative for manufacturing organizations. It enables them to align resources, optimize operations, and deliver on customer expectations in an agile and responsive manner.
Challenges/Problems of Strategic Capacity Planning in Manufacturing
Implementing Strategic Capacity Planning in manufacturing is not without its challenges, and addressing these issues is crucial for its successful execution.
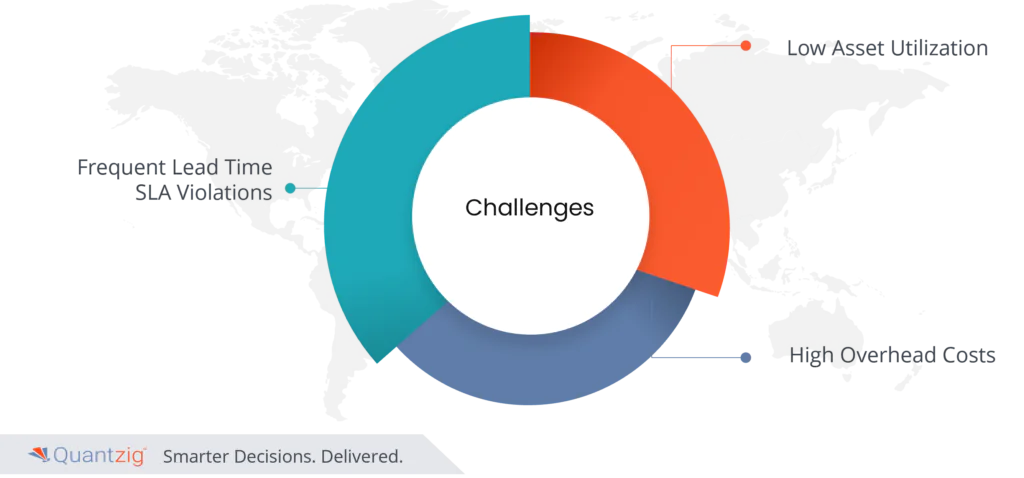
Frequent Lead Time SLA Violations:
A prevalent challenge in strategic capacity planning is the inconsistency in meeting Service Level Agreements (SLAs) for lead times. When the capacity planning process falters, it can lead to production delays, resulting in missed deadlines and dissatisfied customers. These issues often stem from inaccurate demand forecasting or underestimating the time required for production, underscoring the necessity for improved data analysis and robust forecasting tools. Addressing capacity bottlenecks is crucial for effective capacity management.
Low Asset Utilization:
Another significant obstacle is low capacity utilization. Inefficient use of assets—such as underutilized equipment and facilities—can lead to increased operational costs and diminished profitability. To combat this, manufacturers must implement effective capacity planning strategies that optimize resource allocation. Failures often arise from poor scheduling, maintenance issues, or inadequate demand visibility, emphasizing the need for improved operational planning.
High Overhead Costs:
Elevated overhead costs in manufacturing present a considerable challenge to strategic capacity planning. These costs can stem from overstaffing, excessive equipment maintenance, or underused facilities. To mitigate these expenses, manufacturers should focus on streamlining processes, minimizing waste, and enhancing overall operational efficiency. This can be achieved through long-term capacity planning and workforce capacity planning, ensuring that all resources are aligned with capacity vs demand metrics.
By prioritizing accurate data, effective demand forecasting, and efficient resource optimization, manufacturers can overcome these challenges. This approach ensures that capacity planning in operations management delivers its intended benefits, including improved productivity, cost reduction, and enhanced customer satisfaction. Ultimately, embracing scalable growth strategies will enable businesses to adapt to changing market conditions and drive sustainable success.
What are the 5 Best Practices for Manufacturing Capacity Planning?
In manufacturing, efficient utilization of production lines is key to maximizing profits and minimizing costs. Clear goals and robust capacity planning strategies, such as rough-cut capacity planning and resource planning, are essential for managing demand fluctuations effectively.
Best Practices for Manufacturing Capacity Planning:
- Tracking Time and Level of Effort:
Collect data on task durations and refine planning processes for optimal resource allocation. - Identifying Bottlenecks:
Use MES software for real-time visibility to quickly pinpoint and address congestion areas in production. - Scheduling Buffers for L&D:
Allocate time for training to enhance employee skills and foster a culture of learning. - Calculating True Availability:
Analyze employee time usage to accurately assess production capacity and minimize risks of overload or underutilization. - Prioritizing Projects to Allocate Resources:
Set criteria to focus resources on high-priority projects, optimizing utilization and ensuring alignment with business goals.
By integrating these practices, manufacturers can enhance operational efficiency and drive business success in a dynamic environment.
Experience the advantages firsthand by testing a customized complimentary pilot designed to address your specific requirements. Pilot studies are non-committal in nature.
Request a Free Pilot6 Recommendations for Strategic Capacity Planning for Products and Services
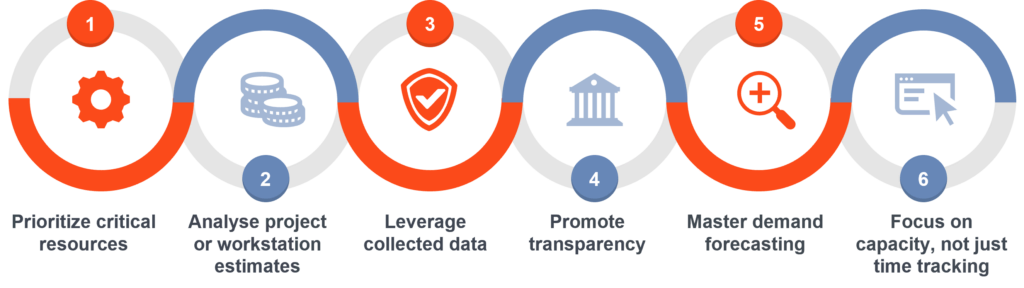

In the landscape of manufacturing, effective capacity planning for products and services is paramount for optimizing production lines and streamlining production processes to bolster profits and mitigate costs. Here’s a comprehensive guide incorporating all the key terms:
To commence your capacity planning endeavor, consider these six strategic recommendations:
1. Prioritize critical resources:
Begin by meticulously assessing the utilization and capacity of key resources, such as machinery and skilled labor. By focusing on high-demand resources initially, you can gain valuable insights into capacity utilization without overwhelming data collection efforts.
2. Analyze project or workstation estimates:
Start by scrutinizing the performance of individual workstations to gauge capacity levels within specific areas of the production floor. This step-by-step approach allows for a gradual understanding of capacity across different production plans and workstations, facilitating targeted improvements.
3. Leverage collected data:
Ensure that the data amassed during capacity planning is actively utilized to drive decision-making and resource optimization efforts. Effective data utilization not only enhances capacity planning accuracy but also fosters a culture of continuous improvement within the organization.
4. Promote transparency and communication:
Foster open communication with employees regarding the objectives and significance of capacity planning initiatives. Transparent communication fosters employee engagement and cooperation, aligning everyone towards common goals of productivity improvement and success.
5. Master demand forecasting:
Invest time in mastering demand forecasting techniques to accurately predict fluctuations in demand patterns. A robust understanding of demand dynamics enables proactive capacity planning, ensuring that resources align with fluctuating production requirements effectively.
6. Focus on capacity, not just time tracking:
While time tracking can offer valuable insights, prioritize capacity assessment over mere clock-watching. Capacity planning should encompass a holistic view of resource availability and utilization, going beyond simple time tracking metrics.
By incorporating these recommendations into your capacity planning strategy, you can establish a robust framework for optimizing production capacity, minimizing bottlenecks, and enhancing overall efficiency across production lines and supply chain capacity.
Quantzig’s Strategic Capacity Planning Solution for a UK-Based Manufacturing Company
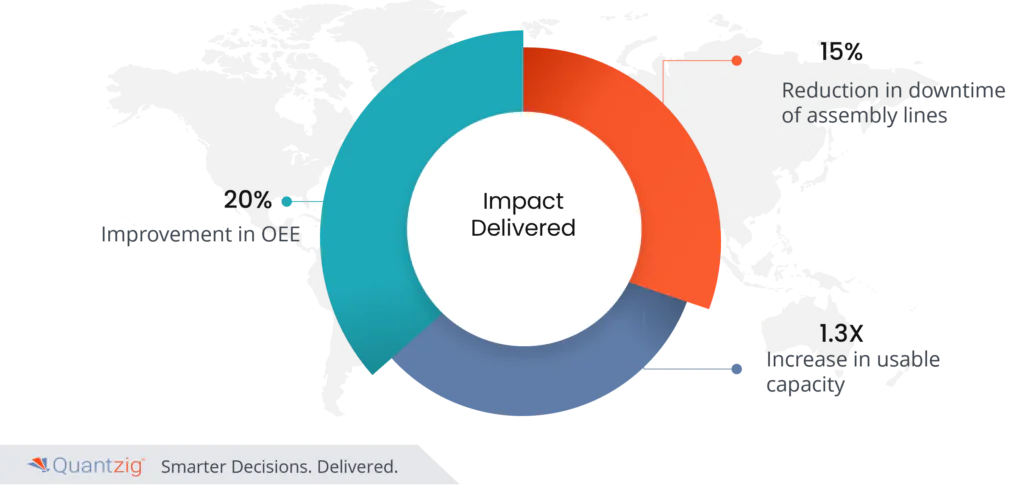
Section | Details |
---|---|
Client Details | Leading manufacturing company operating in the UK and Europe |
Challenges Faced | 1. Frequent lead time SLA violations due to inaccurate demand forecasting and underestimated production time 2. Low asset utilization resulting in higher costs and reduced profitability 3. High overhead costs stemming from overstaffing, unnecessary equipment maintenance, and underutilized facilities |
Solutions Offered | 1. Implemented Capacity Utilization Diagnostics Tool to gain insights into production processes and identify bottlenecks 2. Introduced Intelligent Capacity Allocation Model to optimize production capacity based on demand patterns, minimizing SLA violations and enhancing customer satisfaction 3. Developed CapEx Forecasting Framework to plan capital expenditures precisely, minimizing unnecessary spending and reducing overhead costs |
Impact Delivered | 1. 20% improvement in Overall Equipment Effectiveness (OEE) by optimizing equipment capacity planning and streamlining workflows 2. 15% reduction in downtime of assembly lines through rigorous analysis and proactive maintenance 3. 1.3X increase in usable capacity by aligning personnel and machines with goals and enhancing staff qualifications |
The case study highlights how Quantzig’s solutions helped the manufacturing client overcome challenges related to lead time violations, low asset utilization, and high overhead costs. By implementing advanced tools and models, Quantzig enabled the client to gain insights into production processes, optimize capacity allocation, and plan capital expenditures more effectively. This resulted in significant improvements in OEE, reduced downtime, and increased usable capacity, positioning the client for long-term success in the competitive manufacturing landscape.
Get started with your complimentary trial today and delve into our platform without any obligations. Explore our wide range of customized, consumption driven analytical solutions services built across the analytical maturity levels.
Start your Free TrialConclusion
In conclusion, the imperative of Enhancing Manufacturing Output through Strategic Capacity Planning to Meet Demand cannot be overstated. In an era of rapid technological advancements and market fluctuations, this strategic approach emerges as the bedrock of sustainable success. By optimizing asset utilization, enhancing production throughput, and effectively planning future capital expenditures, manufacturers can navigate challenges with precision and confidence. They can meet customer demands promptly, trim operational costs, and position themselves for growth. As manufacturing continues to evolve, those who embrace strategic capacity planning stand poised to not only survive but thrive, ushering in a future defined by efficiency, profitability, and unwavering customer satisfaction.