Table of Contents
Overview of Warehouse Inventory Management System:
In an increasingly complex supply chain landscape, businesses are turning to Warehouse Inventory Management Systems to streamline operations, cut costs, and enhance overall efficiency. A well-implemented system optimizes inventory levels, improves real-time tracking, and automates workflows, resulting in greater supply chain agility. This blog explores the financial and operational benefits of deploying advanced warehouse management systems, along with how Quantzig’s expertise in predictive analytics enhances supply chain resilience.
Key Takeaways
- Implementing a Warehouse Inventory Management System leads to significant cost savings and enhanced supply chain agility.
- Real-time tracking and automated workflows improve warehouse efficiency and decision-making.
- Advanced warehouse management systems leverage AI and analytics to optimize inventory planning and logistics.
- Quantzig’s expertise in predictive analytics helps businesses stay ahead of market demands and reduce supply chain risks.
- End-to-End Automation drives efficiency, enhances compliance, and ensures seamless operations across the supply chain.
What Is Warehouse Inventory Management?
Warehouse inventory management refers to the process of tracking, organizing, and optimizing inventory within a warehouse to ensure smooth operations and efficient order fulfillment. It involves monitoring stock levels, implementing storage strategies, and leveraging technology to improve inventory accuracy and reduce waste.
By integrating advanced tools such as RFID tracking, IoT sensors, and AI-driven analytics, businesses can achieve real-time visibility into inventory movements, minimize stock discrepancies, and enhance supply chain efficiency. An effective Warehouse Inventory Management System ensures seamless coordination between procurement, storage, and distribution, ultimately improving overall business performance.
Inventory Management vs. Warehouse Management
Inventory management and warehouse management are often used interchangeably, but they serve distinct purposes.
Feature | Inventory Management | Warehouse Management |
---|---|---|
Focus | Forecasting, ordering, and stock allocation | Storage, retrieval, and operational efficiency |
Scope | Raw materials, components, and finished products | Warehouse layout, space optimization, and material handling |
Key Role | Purchasing manager forecasts demand | Warehouse manager oversees daily operations |
Objective | Maintain optimal inventory levels | Enhance warehouse efficiency, reduce costs, and improve fulfillment |
Comparative Analysis: Traditional vs. Advanced Warehouse Inventory Management Systems
Feature | Traditional Warehouse Management | Advanced Warehouse Inventory Management System |
Inventory Tracking | Manual, prone to errors | Real-time tracking with RFID & IoT |
Stock Optimization | Reactive, based on past data | Predictive analytics for demand forecasting |
Order Processing | Labor-intensive | Automated workflows |
Supply Chain Visibility | Limited | Full transparency & supplier coordination |
Cost Savings | Higher operational expenses | Reduced holding, labor, and logistics costs |
Integration | Standalone systems | Integrated with ERP, CRM, and AI analytics |
Demand Forecasting | Based on historical trends | AI-driven predictive modeling |
Error Reduction | High error rates | Automated quality checks |
Financial and Operational Benefits of a Warehouse Inventory Management System
1. Cost Reduction through Improved Inventory Control
- Minimizing Overstock and Stockouts: Over-ordering ties up capital, while stockouts lead to missed sales. A Warehouse Inventory Management System ensures optimal stock levels, reducing excess inventory and associated carrying costs.
- Lowering Holding Costs: By maintaining accurate inventory data, businesses can prevent unnecessary storage expenses.
- Reducing Labor Costs: Automation minimizes manual effort in inventory tracking, order processing, and warehouse management.
- Optimized Procurement Processes: By analyzing historical data, the system helps identify cost-effective suppliers and reduces procurement inefficiencies.
- Decreased Waste and Obsolescence: AI-powered analytics ensure products with shorter shelf lives are sold before expiration, preventing financial loss.
2. Real-Time Tracking for Increased Visibility
- RFID and IoT Integration: Advanced systems use RFID (Radio Frequency Identification) and IoT sensors to provide instant inventory updates, reducing discrepancies and theft.
- Demand Forecasting: Real-time tracking enables businesses to predict demand fluctuations and adjust stock levels accordingly.
- Supply Chain Transparency: Improved visibility ensures better decision-making, reducing the risk of disruptions.
- Enhanced Customer Satisfaction: Faster fulfillment and accurate tracking improve customer service levels, leading to increased brand loyalty.
- Proactive Issue Resolution: Alerts and notifications allow businesses to address supply chain disruptions before they escalate.
3. Automated Workflows for Operational Efficiency
- Order Processing Automation: A Warehouse Inventory Management System automates order picking, packing, and shipping, reducing fulfillment errors.
- Optimized Space Utilization: Advanced algorithms help maximize storage capacity and minimize waste.
- Seamless Supplier Coordination: Automated reordering ensures inventory replenishment aligns with demand.
- Integration with ERP and CRM Systems: Ensures smooth data exchange across business functions for better decision-making.
- Enhanced Workforce Productivity: Automating repetitive tasks allows employees to focus on high-value activities.
Best Practices for Warehouse Inventory Management in 2025
Effective warehouse inventory management in 2025 revolves around automation, data-driven decision-making, and strategic collaboration. By integrating AI-powered analytics, real-time tracking technologies, and automated workflows, businesses can reduce errors, optimize stock levels, and enhance operational efficiency.
Key Best Practices:
- Implement Automated Cycle Counting – Regular, systematic inventory checks ensure accuracy without disrupting daily operations.
- Leverage AI for Demand Forecasting – Predictive analytics optimize inventory levels, reducing stockouts and excess storage costs.
- Adopt RFID and IoT for Real-Time Tracking – These technologies enhance visibility, minimize discrepancies, and streamline logistics.
- Optimize Warehouse Layout and Storage – Strategic organization improves space utilization, reduces retrieval times, and enhances efficiency.
- Integrate Warehouse Management Systems with ERP – Seamless data exchange improves inventory accuracy, supplier coordination, and order fulfillment.
- Enhance Supplier Collaboration – Real-time data sharing and automated reordering prevent supply chain disruptions.
- Utilize Robotics and Automation – Automated picking, packing, and sorting increase efficiency and reduce labor costs.
In 2025, warehouse inventory management is evolving with cutting-edge technologies and strategic approaches that drive efficiency and cost savings. Businesses that adopt AI-driven analytics, automation, and real-time tracking will gain a competitive edge by minimizing errors, improving supply chain agility, and enhancing customer satisfaction. Partner with Quantzig to implement these best practices and revolutionize your warehouse operations with data-driven solutions.
Quantzig’s Expertise in Enhancing Supply Chain Resilience
Quantzig leverages predictive analytics and AI-driven solutions to enhance the effectiveness of advanced warehouse management systems. Our data-driven approach ensures businesses achieve:
Quantzig’s Expertise
Data models predict demand patterns, minimizing waste and shortages.
AI-powered insights help businesses respond proactively to supply chain disruptions.
Predictive analytics improves transportation planning, reducing fuel and logistics costs.
Identifies potential bottlenecks and supply chain vulnerabilities before they impact operations.
Enhances warehouse efficiency, logistics coordination, and demand forecasting to maximize profitability.
Future Trends in Warehouse Inventory Management
The future of warehouse inventory management is being shaped by cutting-edge technologies and innovative strategies. Businesses are moving toward AI-driven analytics, automation, and sustainable practices to enhance operational efficiency and adaptability. Here are some key trends that will define the next generation of Warehouse Inventory Management Systems:
- AI-Powered Predictive Analytics: Future Warehouse Inventory Management Systems will use AI to forecast demand with even greater accuracy.
- Blockchain for Supply Chain Transparency: Secure, tamper-proof records will enhance supply chain trust and traceability.
- Autonomous Warehouse Operations: Robotics and automation will reduce reliance on human intervention, increasing operational speed.
- Cloud-Based WMS Solutions: Cloud integration will allow remote warehouse monitoring and seamless data access.
- Sustainability and Green Warehousing: AI-driven systems will optimize energy use and reduce waste, supporting environmental goals.
Conclusion
Businesses seeking to stay competitive in a dynamic supply chain environment must invest in advanced warehouse management systems. A Warehouse Inventory Management System enables cost-efficient operations, real-time tracking, and automation-driven workflows. With Quantzig’s AI-powered analytics, businesses can achieve greater supply chain resilience and agility, ensuring long-term success.
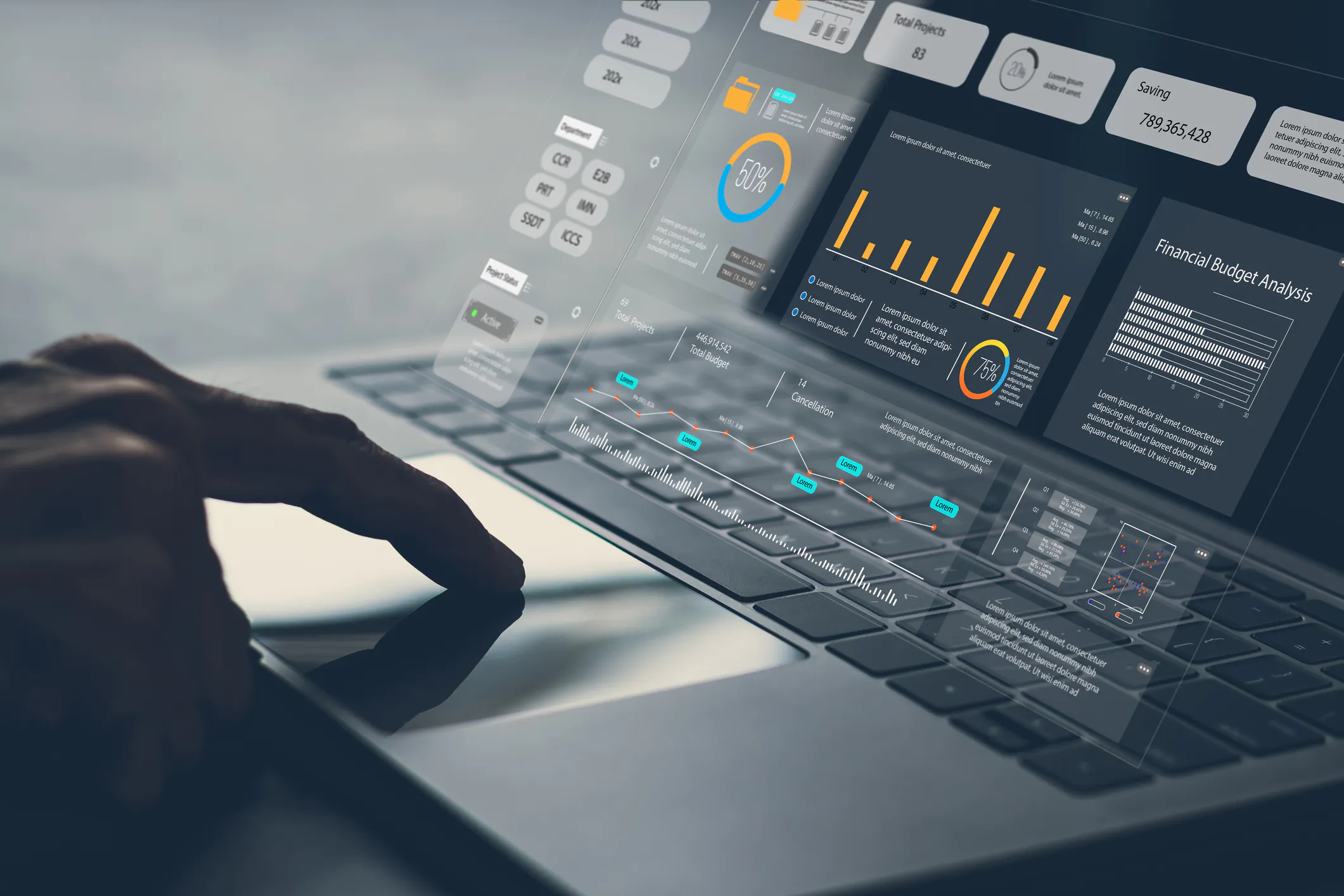
Ready to transform your warehouse operations? Contact Quantzig today for a tailored analytics-driven approach to warehouse management!
Request a pilot