In this digital era, business intelligence tools help organizations with valuable data resources that can be utilized to accomplish business goals by making essential strategic decisions. BI tools can measure and analyze various customer interactions such as chat support, voice calls, and email support to understand purchasing habits, customer preferences, and market trends to increase the conversion ratio. The article offers strategic insights and practical applications, guiding professionals towards a synergy between cutting-edge BI technologies and proactive maintenance strategies, fostering a paradigm shift in how businesses approach asset management for sustainable growth in today’s competitive markets.
Table of Contents
Key Benefits of integrating business intelligence into maintenance strategies:
Incorporating Business Intelligence (BI) into maintenance strategies yields a myriad of benefits, revolutionizing how organizations manage their assets and enhancing overall productivity. The top five advantages of this integration are as follows:
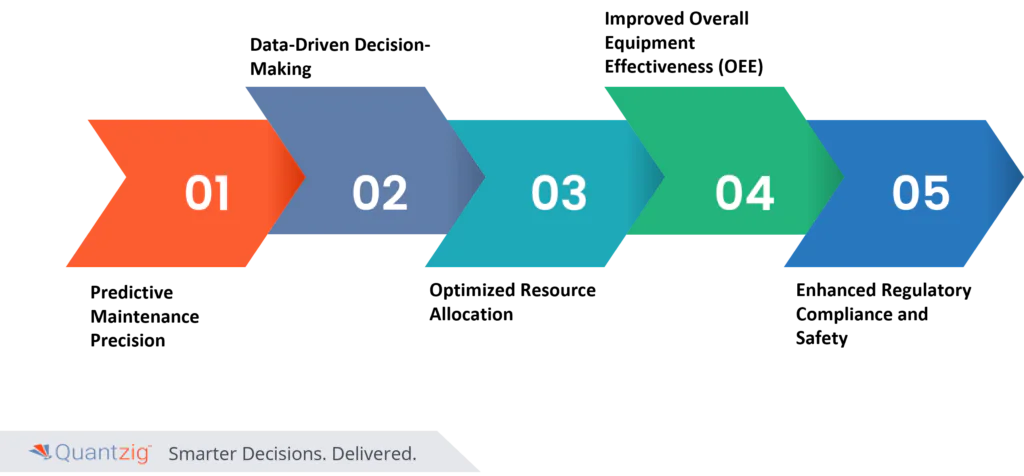
- Predictive Maintenance Precision:
By integrating BI tools into maintenance strategies, organizations gain the ability to predict equipment failures with unparalleled precision. BI leverages historical data, sensor readings, and machine learning algorithms to foresee potential issues, allowing proactive interventions before breakdowns occur. This predictive approach minimizes unplanned downtime, extends asset lifecycles, and optimizes maintenance schedules, ultimately boosting productivity.
- Data-Driven Decision-Making:
BI empowers decision-makers with comprehensive insights derived from real-time data analytics. Maintenance strategies guided by accurate and up-to-date information enable organizations to make informed decisions. Whether it’s allocating resources efficiently, prioritizing critical repairs, or optimizing preventive maintenance schedules, the integration of BI ensures that decisions are rooted in data, leading to enhanced operational efficiency and productivity gains.
- Optimized Resource Allocation:
Business Intelligence enables a more strategic allocation of resources by providing a holistic view of asset performance. By analyzing data on equipment health, usage patterns, and historical maintenance records, organizations can allocate resources effectively. This optimization extends beyond manpower to include spare parts inventory management, reducing costs associated with overstocking or emergency procurements. This streamlined resource allocation contributes significantly to increased productivity.
- Improved Overall Equipment Effectiveness (OEE):
Integrating BI into maintenance strategies directly impacts Overall Equipment Effectiveness (OEE), a key metric in measuring manufacturing efficiency. BI tools enable continuous monitoring of equipment performance, identifying and addressing factors contributing to downtime, inefficiencies, or suboptimal utilization. As organizations fine-tune their maintenance approaches based on BI insights, OEE improves, leading to increased productivity and enhanced competitiveness.
- Enhanced Regulatory Compliance and Safety:
BI-driven maintenance strategies facilitate compliance with industry regulations and safety standards. Through real-time monitoring and data analytics, organizations can ensure that equipment meets regulatory requirements and operates within safety parameters. Proactively addressing compliance issues not only mitigates risks but also contributes to a more secure and stable operational environment. Compliance and safety adherence, supported by BI insights, instill confidence among stakeholders and positively impact overall productivity.
In conclusion, the integration of Business Intelligence into maintenance strategies delivers a transformative impact on organizational productivity. From predictive maintenance to data-driven decision-making and optimized resource allocation, the benefits of leveraging BI in maintenance strategies are multifaceted, providing a competitive edge in today’s dynamic business landscape.
Challenges while implementing business intelligence into maintenance strategies:
The maintenance planning process is a multifaceted approach encompassing predictive maintenance, parts planning, and downtime management. This intricate process plays a pivotal role in ensuring operational efficiency and equipment reliability. However, its complexity can lead to substantial costs if not meticulously executed.
- Predictive Maintenance Precision:
The accuracy of predictive maintenance strategies hinges on advanced analytics and data-driven insights. Failure to harness these technologies can result in unnecessary downtime and increased maintenance expenses.
- Strategic Parts Planning:
Efficient parts management involves anticipating the needs of machinery components. Inadequate planning may lead to delays in obtaining critical parts, amplifying downtime and escalating costs.
- Downtime Mitigation Strategies:
Effective downtime management demands a well-coordinated plan to minimize disruptions. Inadequate planning may result in extended downtime, impacting production schedules and incurring additional labor and operational expenses.
Conclusion:
In conclusion, integrating Business Intelligence (BI) into maintenance strategies emerges as a paramount initiative for optimizing productivity. Leveraging BI tools provides organizations with real-time insights, predictive analytics, and data-driven decision-making capabilities. This synergy empowers maintenance teams to proactively address issues, reduce downtime, and enhance overall operational efficiency. By harnessing BI’s analytical prowess, businesses can streamline maintenance processes, allocate resources judiciously, and foster a proactive maintenance culture. Ultimately, the integration of BI into maintenance strategies not only augments asset reliability but also cultivates a competitive edge by fostering a data-centric approach that aligns seamlessly with contemporary demands for precision and efficiency.
Success Story:
Optimizing Operational Excellence: A Business Intelligence Infusion into Maintenance Strategies
Client details:
Industry Leader in Manufacturing Solutions located in the USA
Client Sector: Manufacturing
Challenges: Significant downtimes, communication gaps in maintenance schedules, and lack of effective Root Cause Analysis (RCA).
Solution: Integration of Business Intelligence (BI) into maintenance strategies.
Challenges Faced by the Client:
- Unplanned Downtimes Impact:
The client encountered substantial downtimes attributable to unplanned maintenance and device breakdowns, adversely affecting operational continuity and efficiency.
- Communication Challenges with Dispersed Data:
The absence of a centralized platform for maintenance schedules and replans hindered effective communication within teams. This decentralized approach made it challenging for teams to promptly relay and adapt to changes in the maintenance schedule, exacerbating downtime issues.
- Storyboarding Deficiency for RCA:
The inadequacy in storyboarding the maintenance schedule data posed impediments to Root Cause Analysis (RCA). Without a visually organized narrative, identifying patterns and key factors contributing to breakdowns became arduous, impeding the development of effective preventive strategies and perpetuating the cycle of unplanned downtimes.
Solutions Offered by Quantzig:
- Rapid Deployment with Azure AI:
Leveraging Azure AI systems, we expedited the development of a robust predictive maintenance solution, enabling implementation within weeks. This solution seamlessly integrated with the client’s data lake and efficiently processed machine sensor data, laying the foundation for proactive maintenance strategies.
- Custom Planning Tool for Enhanced Collaboration:
We introduced a bespoke planning tool that simplified the predictive maintenance planning process. This custom tool facilitated easy collaboration among multiple teams and plants, streamlining the coordination of parts availability and maintenance labor schedules. This centralized approach significantly reduced complexities and enhanced overall planning efficiency.
- Storyboarded BI Dashboard for RCA:
Our approach included storyboarding the Business Intelligence (BI) dashboard and providing a visual narrative to simplify Root Cause Analysis (RCA). This enhancement enabled stakeholders to easily comprehend the factors contributing to downtime and line inefficiencies. The BI dashboard served as a strategic tool for decision-makers, offering clear insights into risk areas and fostering a proactive approach to mitigate potential issues, thereby optimizing operational performance.
Impact Delivered:
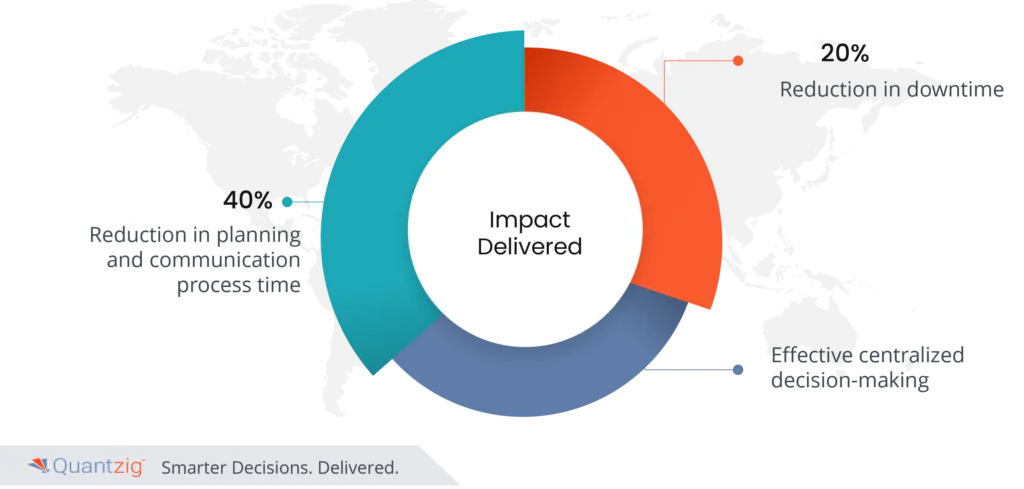
- Reduction in downtime by 20%
- Reduction in planning and communication process time by 40%
Technologies Implemented:
Azure Synapse, power platforms
Unlock Your Operational Potential!
Discover how our tailored solutions can propel your business toward unprecedented productivity and efficiency. Contact us today for a personalized consultation on integrating BI into your maintenance framework.
Related Articles
- 3 Amazing Retail Analytics Trends You May Not Have Known
- 3 Best Practices Businesses for Managing a Successful Retail Analytics Campaign
- 3 Ways to Improve Retail Price Optimization Strategy
- 30% Reduction in Employee Turnover Rates Achieved by Retail Chain Through the Implementation of Turnover Prediction Models