In the dynamic landscape of industrial manufacturing, achieving optimal efficiency in chemical production and capacity planning is paramount for sustained success. Capacity planning in chemical manufacturing involves recognizing the production capacity that the facilities can handle and strategic planning for future capacity requirements. This process is crucial to ensuring that the facility can fulfill customer needs while remaining profitable. In this article, we will discuss the significance of capacity planning in chemical manufacturing, the possible challenges faced during this entire process, and how to overcome those challenges. Join us on a journey toward operational excellence, where strategic foresight meets industrial manufacturing optimization.
Table of Contents
Importance of Capacity Planning for Chemical Manufacturing Optimization:
- Capacity planning stands as a pivotal facet within chemical manufacturing facilities, offering the means to streamline production resources and ensure profitability while meeting customer demands. The scheduler, armed with insights into the facility’s production capacity, strategically plans for the allocation of necessary resources, encompassing raw materials, equipment, and labor. This meticulous planning is instrumental in adapting to changes in product demand, with a keen analysis of demand forecasts enabling the proactive adjustment of resources to avert bottlenecks or delays that may jeopardize business opportunities.
- Furthermore, the significance of capacity planning in chemical manufacturing extends to cost optimization. By judiciously aligning production resources, facilities can sidestep the pitfalls of overproduction, mitigating the risks of inventory waste. Simultaneously, this planning shields against underproduction, safeguarding against missed business prospects. In essence, capacity planning emerges as a linchpin for agile and cost-effective operations in chemical manufacturing environments.
Challenges in implementing Capacity Planning for Chemical Manufacturing:

- Resource-Intensive Analysis:
Capacity planning in manufacturing scheduling demands extensive human involvement, consuming several weeks of intensive manual analysis. This encompasses evaluating production volumes, resource availability, and demand fluctuations to ensure precision in decision-making.
- Risk of Errors:
The prolonged manual engagement in the analysis and decision-making process increases the vulnerability to errors. Fatigue and the intricate nature of the task may contribute to oversights or miscalculations, potentially impacting the accuracy of capacity planning.
- Operational Implications:
Mistakes in capacity planning can reverberate throughout the manufacturing process, leading to disruptions, delays, and compromised operational efficiency. In an era emphasizing precision and streamlined processes, the inherent challenges of manual analysis underscore the need for technological solutions to enhance accuracy and efficiency in manufacturing scheduling.
Conclusion:
In conclusion, the exploration of strategic chemical production and capacity planning unveils a roadmap for industrial manufacturing optimization. The imperative of aligning production resources with demand, leveraging advanced technologies, and embracing data-driven decision-making emerges as a central theme. As organizations navigate the intricacies of chemical manufacturing, the significance of proactive capacity planning becomes evident, offering a shield against potential bottlenecks and facilitating adaptability to dynamic market demands.
The call for excellence resonates not only in the avoidance of overproduction and underproduction pitfalls but also in the broader context of minimizing costs and maximizing operational efficiency. This article serves as a guide for industry leaders, urging them to embrace innovation, automation, and strategic foresight to propel their facilities toward a future where precision, efficiency, and optimization converge for sustained success in the competitive landscape of industrial manufacturing.
Success Story:
“Revolutionizing Chemical Manufacturing: A Quantzig Success Story in Strategic Production and Capacity Planning Optimization”
Client details:
A leading chemical manufacturing company located in the USA
Challenges Faced by the Client:
- Traditional Tools and ERP Systems:
The initial capacity planning relied on conventional productivity tools integrated within ERP systems, representing a method that proved to be labor-intensive and less efficient.
- Extended Planning Cycles:
The inherent limitations of the traditional approach manifested in prolonged planning cycles, averaging 3-4 weeks for each iteration. This duration posed a challenge in meeting the dynamic demands of manufacturing in a rapidly evolving market.
- Client Demand for Agility:
Recognizing the imperative for adaptability, the client articulated a strategic shift. They sought to compress the planning timeline to less than a week, emphasizing the need for swift adjustments to cater to the changing landscape of manufacturing needs. This shift underscored the industry’s commitment to enhancing efficiency and responsiveness in capacity planning processes.
Solutions Offered by Quantzig:
- Integrated End-to-End Production Planning Tool:
Our team developed a comprehensive end-to-end production planning tool seamlessly integrated with clients’ existing ERP systems. Leveraging the Power platform, the tool facilitated a cohesive workflow, ensuring a streamlined connection between various stages of production planning.
- No-Code Solutions for Simplified Processes:
The innovative approach involved the use of quickly buildable, no-code solutions on Power platforms. This strategic choice not only simplified the complexity of material planning, capacity planning, Long-Range Planning (LRP), and capacity constraint planning but also enhanced the adaptability of the solution for efficient deployment and customization.
- Significant Time Reduction and Workflow Optimization:
The implemented solution yielded remarkable results, reducing the traditional planning cycle from weeks to mere days. This transformative optimization was attributed to the integrated, no-code approach, enabling swift decision-making and adjustments. The tool’s efficiency not only met the client’s objective of rapid adaptability but also underscored the potential of technology-driven solutions in revolutionizing production planning workflows for enhanced agility and responsiveness.
Impact Delivered:
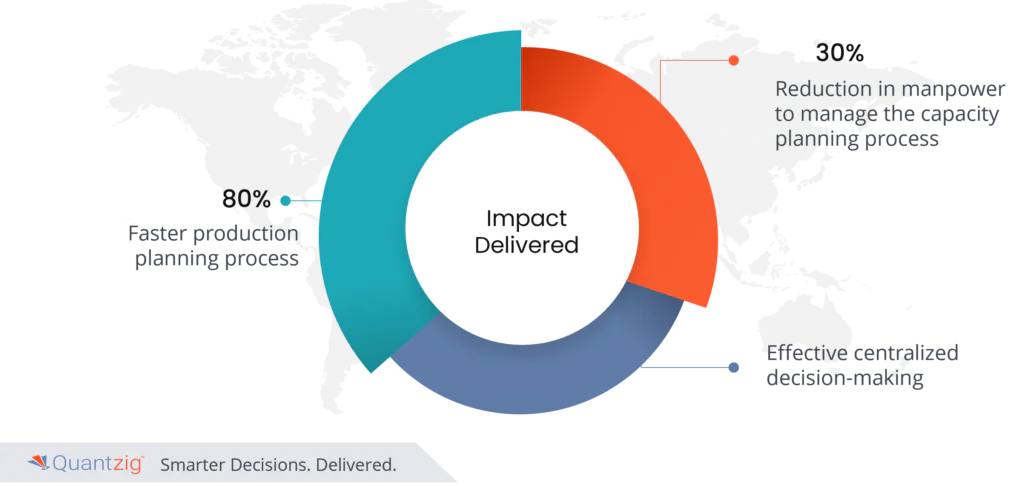
- 80% faster production planning process.
- 30% reduction in manpower to manage the capacity planning process
Discover how Quantzig, through innovative solutions and strategic expertise, helped the client excel in strategic chemical production and capacity planning. Explore the full case study for insights into transforming manufacturing processes and achieving excellence. Contact us today to embark on your journey toward optimized industrial manufacturing.
Related Articles
- 3 Amazing Retail Analytics Trends You May Not Have Known
- 3 Best Practices Businesses for Managing a Successful Retail Analytics Campaign
- 3 Ways to Improve Retail Price Optimization Strategy
- 30% Reduction in Employee Turnover Rates Achieved by Retail Chain Through the Implementation of Turnover Prediction Models