Written By: Sudeshna Ghosh
In the realm of manufacturing, where diverse processes span across geographies, optimizing operations is a monumental challenge. The importance of this endeavor cannot be overstated, as manufacturing companies grapple with substantial expenditures and the intricacies of streamlining processes. Leveraging analytics for supply chain optimization emerges as the beacon of change, offering solutions to reduce cost leakages and drastically improve profitability.
Don’t miss out on this vital resource – read on to revolutionize your product manufacturing practices and propel your business to new heights!
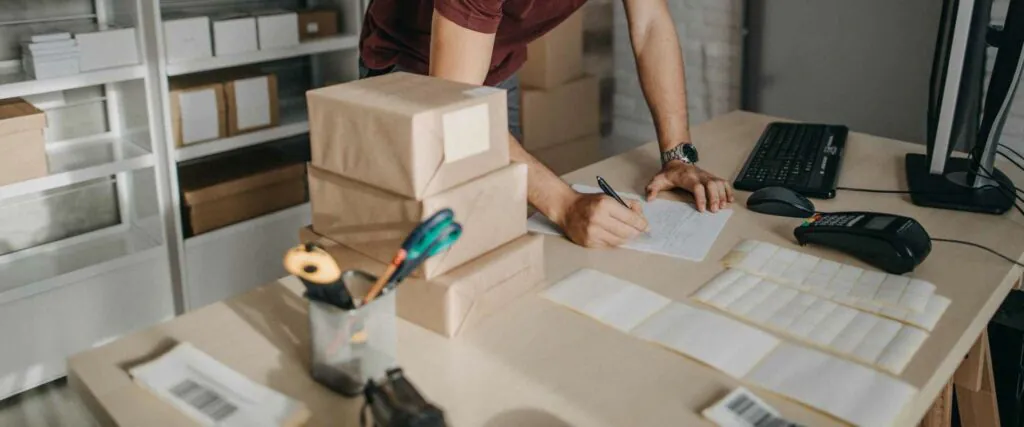
Table of Contents
Challenges in Implementing Analytics in Manufacturing:
- Data Quality Hurdles: The manufacturing landscape deals with data from various sources and systems, often of insufficient or poor quality. Ensuring accuracy and completeness becomes a significant challenge.
- Complexity in Supply Chains: Modern supply chains are intricate, involving multiple stakeholders. Managing this complexity and optimizing the entire network poses a major challenge for manufacturers.
- Production Schedule Optimization: Balancing factors like machine capacity, labor availability, order priorities, and setup times in production schedules can lead to conflicts, disrupting operations.
- Balancing Cost and Performance: The pressure to reduce manufacturing costs while maintaining optimal performance can be challenging, potentially compromising quality or efficiency.
- Sustainability and Social Responsibility Standards: Adhering to sustainability and social responsibility standards requires changes in processes, materials, and sourcing, presenting additional challenges for manufacturers.
Benefits of Implementing Analytics in Manufacturing:
- Cost Reduction and Profitability: Analytics enables the identification of inefficiencies, optimizing resource utilization, reducing material waste, and streamlining production processes. These directly impact a company’s bottom line and profitability.
- Quality Control: Real-time quality monitoring helps identify defects early in the production process, reducing rework, scrap, and the likelihood of defective products reaching customers.
- Data-Driven Decision-Making: Analytics provides data-driven insights empowering decision-makers to make informed choices about resource allocation, production scheduling, and supply chain management.
- Predictive Maintenance: Analytics, particularly predictive maintenance, identifies machinery issues before costly breakdowns occur, minimizing unplanned downtime.
- Sustainability Goals: Analytics identifies ways to reduce waste, energy consumption, and emissions, aligning manufacturing practices with sustainability goals.
- Competitive Edge: Companies effectively using analytics gain a competitive edge, responding to market changes more quickly, adapting to customer demands, and delivering products with better quality and lower costs.
- Improved Efficiency and Customer Satisfaction: Optimized manufacturing processes lead to quicker delivery times, higher product quality, and improved customer satisfaction, ultimately enhancing customer loyalty.
Quantzig partnered with a US-based client facing challenges despite substantial investments in assets and technologies. By analyzing current and past asset and technology utilization scenarios, Quantzig identified underutilized resources and provided downsizing strategies. The result was a 12% boost in manufacturing output, a twofold improvement in customer satisfaction, and a centralized data-backed strategy for budget investments.
In conclusion, the article explores the transformative power of analytics in manufacturing, addressing challenges, showcasing benefits, and presenting a real-world case study. It underscores the pivotal role analytics plays in shaping the future of manufacturing, offering a competitive edge and paving the way for enhanced efficiency and profitability.