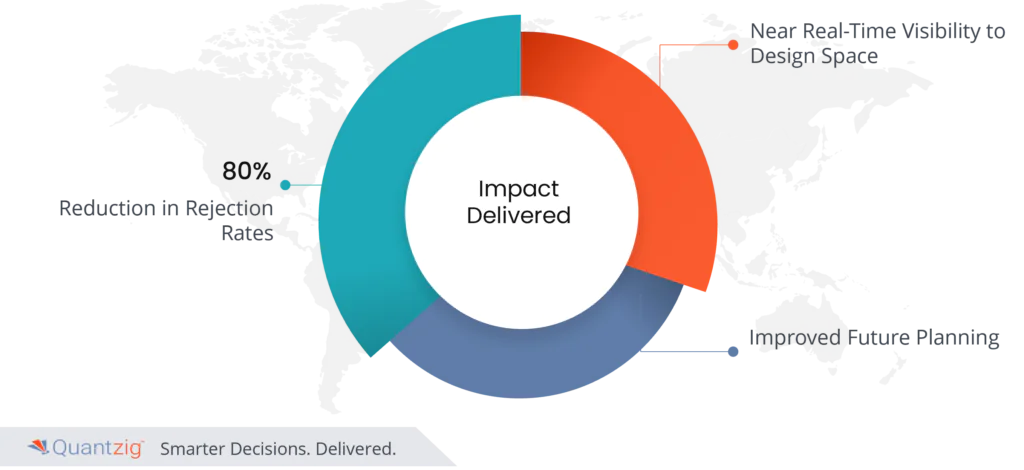
Table of Contents
Summary
Client Details: The UK-based pharmaceutical manufacturer, with more than $1 Bn market capitalization.
Challenges: Quantzig recently partnered with the client to address their challenges of high rejection rates and the need to rationalize their manufacturing practices. The client was facing consistent rejection of product batches due to deviations in critical quality attributes. This resulted in significant financial losses and impacted product availability.
Solutions: Quantzig’s solution involved leveraging sensor data to identify the root causes of the deviations and optimize manufacturing processes. By establishing an infrastructure to aggregate sensor data and employing advanced analytics techniques, we enabled them to reduce rejection rates, improve manufacturing optimization practices, and enhance overall operational efficiency.
Impact Delivered
All of the above initiatives resulted in:
- 80% Reduction in rejection rate
- Near real-time visibility to design space
- Improved future planning
Industry Overview
- The UK-based pharmaceutical manufacturing industry holds immense importance within the country’s healthcare landscape. It encompasses various activities, such as research, development, manufacturing, and distribution of pharmaceutical products.
- Manufacturing optimization plays a crucial role in this industry, enabling companies to streamline processes, enhance productivity, and ensure consistent product quality. By implementing advanced technologies, data analytics, and process improvements, manufacturers can reduce costs, minimize waste, and improve overall operational efficiency.
- Manufacturing optimization also facilitates the timely delivery of high-quality medications, supports regulatory compliance, and fosters innovation. It is a key driver for enhancing competitiveness, meeting market demands, and sustaining the growth of the UK pharmaceutical manufacturing industry.
About the Client
- The UK-based pharmaceutical manufacturer, with more than $1 Bn market capitalization was facing consistent rejection in their product batches by the regulatory agency because of deviations in critical quality attributes. These deviations indicated a failure to meet the required standards.
- The continuous rejections led to significant financial losses for the client, with a total loss of over $300K in terms of product cost. This financial impact further exacerbated the availability issues faced by the client, affecting their ability to meet the market demand for the product.
Challenges
- After consulting with its quality assurance team, the client obtained confirmation that the material quality used in its manufacturing process met the defined standards. Through meticulous testing and analysis, they determined that the deviations in critical quality attributes were not attributable to the raw materials themselves. This finding allowed them to focus their attention on other aspects of the production process, such as equipment, procedures, or personnel, to identify the root causes of the deviations.
- To identify the root cause of the deviations in critical quality attributes, the client turned to their sensor data for insights. However, they encountered a significant challenge due to the sheer volume of data being generated daily across multiple machines. With millions of rows of data to analyze, it became impractical for them to manually sift through the data and extract meaningful patterns or correlations. The overwhelming amount of data posed a hindrance to their efforts to pinpoint specific issues in the manufacturing process.
- Recognizing the challenge posed by the vast amount of sensor data, they sought a solution that could aggregate and analyze the data effectively. They required a system capable of deriving key performance indicators (KPIs) and trends from the data, providing actionable insights for decision-making. Additionally, they desired a solution with future preparation capability, enabling them to anticipate potential issues and proactively address them. This solution would empower them to gain a comprehensive understanding of their manufacturing processes, identify areas for improvement, make informed decisions for manufacturing optimization, and maintain consistent product quality.
Solutions
- Quantzig played a pivotal role in driving manufacturing optimization by establishing an infrastructure capable of aggregating data from a wide array of sensors. This infrastructure served as a central hub, efficiently collecting, and integrating data streams originating from multiple sensors across the manufacturing environment. By consolidating the sensor data into a unified platform, we enabled the client to gain comprehensive visibility into their operations. This empowered them to analyze the data and identify key patterns, trends, and anomalies that could impact manufacturing efficiency.
- To refine the manufacturing optimization process, we engaged in extensive brainstorming sessions with subject matter experts (SMEs). Together, we identified the key performance indicators (KPIs) that were crucial for the client’s specific manufacturing process. With these KPIs in mind, we developed a system that could generate the desired metrics from the abundant data available. Leveraging correlation analytics, we not only identified the existing KPIs but also discovered new indicators that could contribute to more efficient tracking and performance evaluation. This comprehensive approach allowed them to gain deeper insights into their operations, monitor critical metrics accurately, and make data-driven decisions for manufacturing optimization.
- Then we built a framework to identify the root cause of the current deviation. By leveraging this framework, we were able to uncover patterns, anomalies, and potential correlations within the data that could shed light on the underlying causes of deviation. Through a systematic analysis of various factors such as process parameters, equipment performance, and environmental conditions, we aimed to pinpoint the precise root cause of the deviation. This enabled the client to implement targeted corrective actions and further optimize their manufacturing processes for improved efficiency and quality.
- To ensure manufacturing optimization, we implemented a sophisticated mechanism that involved continuous monitoring of process parameters against defined SLAs. This mechanism utilized real-time data from sensors and other monitoring devices to track and analyze the performance of critical process parameters. By comparing the actual values with the predefined SLAs, we could identify any deviations or anomalies that may impact manufacturing efficiency. This proactive monitoring approach enabled us to swiftly detect any potential issues or deviations, allowing for immediate corrective actions to be taken.